「無駄」の削減に繋げる!動線から考える工場レイアウト改善の基本と考え方
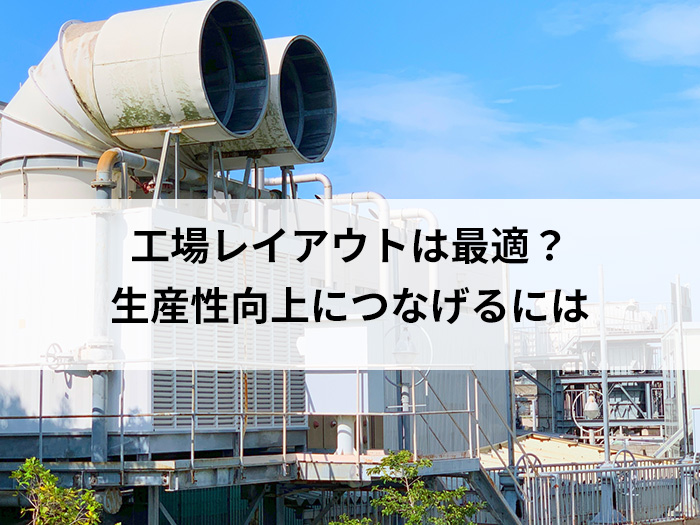
最終更新日:
工場のレイアウトは、生産性向上に直結する重要な要素です。本記事では、特に動線を中心に効率的なレイアウト改善の基本と考え方を解説します。動線の見直しや設備の配置変更により、安全で効率的な作業環境を整えるためのポイントを具体的に紹介し、全体的な業務効率化と生産性向上につなげる方法を考察します。
工場のレイアウトが抱える課題
工場のレイアウトが抱える課題は多岐にわたります。まず、動線の複雑さが挙げられます。複数の設備や部門が適切に配置されていない場合、作業員は不要な移動を強いられることが多く、時間のロスが発生します。このような非効率な動線は、作業のスピードを低下させる主要因となるため、その見直しが重要です。
さらに、保管スペースと作業エリアの配置も問題になることがあります。出荷エリアから遠く隔たった保管スペースでは、商品の取り扱いや出荷が煩雑になり、ミスが増えるリスクを助長します。また、コスト面でも無駄が生じやすくなります。加えて、設備と作業場の距離が遠くなると、作業者間のコミュニケーションが不十分になり、情報共有が滞る場合もあります。
加えて、工場内のデッドスペースの存在も無視できません。デッドスペースを削減し、すべてのエリアを有効活用することが求められます。適切なレイアウトが整っていないと、物品や作業者が互いに干渉し合う事態も起こり得ます。このような課題は、全体の生産性に影響を及ぼすため、早急な改善が必要です。課題を把握し、根本的な解決を目指して積極的な取り組みをすることが求められます。
本稿では、この課題を改善するための方法を詳しく紹介していきます。
「無駄」の削減に繋がる工場レイアウト改善「4つの原則」
工場内のレイアウトは、その中で製造される商品や機械、工程が変わる度に、見直しをかけるのが理想です。日々の製造に追われている工場の中には、長きに渡ってレイアウトを変えないところも多く見受けられます。しかし製造商品や時代のニーズに合わない工場は、作業者の負担を増やす可能性を秘めているため、事故の起こらない安全性を高める上でも、定期的な見直しが必要となります。今回は、工場レイアウト改善をする際に欠かせない「4つの原則」を紹介していきます。
流れの原則
工場のレイアウト改善における流れの原則は、効率的な作業工程の構築に向けた基盤となります。この原則を実践するためには、作業の流れに従い、必要な人や物がスムーズに移動できるように配置を最適化することが求められます。具体的には、製品の製造に関わる各ステーションや作業者の動きを視覚化し、どのように流れるべきかを明確にする必要があります。
例えば、特定の作業工程が多くの作業者を経由する場合、無駄な移動や時間の浪費が発生しやすくなります。このような無駄は、工程間を直線で繋ぐことで解消できます。さらに、必要な資材や道具が近くに配置されることで、作業者の動きを最小限に抑え、効率的な作業が可能となります。このような流れの原則に基づく改善は、結果的に生産性の向上に寄与することが期待されます。
また、レイアウトを見直す際には、客観的なデータに基づく分析が重要です。生産ラインを観察し、実際に作業を行っている様子を確認することで、無駄な動きや遅延の要因を特定します。このようなアプローチを通じて、レイアウトの改善案を検討する際には、実際の作業フローを反映させることが不可欠です。さらに、定期的な見直しと改善を行うことで、流れの原則を維持し続けることができ、柔軟で効率的な工場運営が実現できます。
このように、流れの原則に基づいた工場レイアウトの改善は、効率的な作業環境を整えるための重要な第一歩であり、継続的な改善を図ることで、さらなる持続可能な生産性向上に繋がるのです。
スペース効率の原則
スペース効率の原則は、工場や倉庫などの施設設計において重要な考え方です。スペースを有効に活用することで、従業員の作業効率が向上し、無駄なコストや時間の削減が実現可能となります。具体的には、必要な設備や機械を適切に配置し、デッドスペースを最小限に抑えることが求められます。また、将来の拡張や変化を見越して、フレキシブルなスペース設計を行うことも重要です。
効率的なスペース使用を実現するためには、まず初めに現状調査が必要です。この段階では、スペースの使用状況や効率を詳細に分析し、どこに無駄があるのかを把握します。たとえば、工場内の特定エリアが使用されていない場合、そこを改善することで新たな作業スペースを創出できる可能性があります。また、動線を最適化することで、従業員が移動する距離を短縮し、作業のスピードアップに繋がります。
さらに、スペース効率を高めるためには、物品の保管方法や流通の見直しが必要です。高頻度で使用される物品は作業エリアに近づけ、アクセスの良い場所に配置することが勧められます。一方で、使用頻度の低い物品はデッドスペースとして配置し、必要時にアクセスできる形にすることで、効率的なスペース利用を図ります。
最終的に、スペース効率の原則を導入することは、工場の生産性を高め、コスト削減を実現するための基盤となります。定期的にレイアウトを見直し、状況に応じた改善策を講じることで、長期的な運用効率を確保できるのです。したがって、スペース効率を考慮した設計は、企業全体の競争力を高める要素となるでしょう。
管理容易の原則
管理容易の原則は、工場や生産ラインでの作業を円滑に行うために不可欠な要素です。この原則では、管理しやすいレイアウトや設備の配置を優先し、作業者や管理者が効率的に業務を行える環境を整えます。具体的には、作業フローの可視化や、作業の過程で必要とされる機器や資材の整備が重要です。作業者が必要な道具をすぐに把握できることで、効率が向上し、無駄な移動を減少させることが可能となります。
さらに、管理容易の原則に基づくレイアウトでは、手順や規則が明確であることが求められます。例えば、各作業ステーションの役割を明確にし、作業者が意識するべきポイントやプロセスを具体化することで、業務が円滑に進みます。このように、標準化やマニュアルの整備も不可欠な要素となります。
実際の成功例として、大手製造業では定期的なトレーニングを実施し、管理方法を統一しています。その結果、作業者間の情報共有が活発になり、問題解決が迅速に行えるようになっています。また、作業環境が整備されることで、作業者は自信を持って業務に取り組むことができ、モチベーションの向上にも繋がります。
最終的に、管理容易の原則を取り入れることで、企業は生産性の向上やコストの削減、さらには労働安全の確保も実現できるため、継続的な改善に向けた取り組みが重要です。この原則が根付くことで、組織全体のパフォーマンス向上が期待できるでしょう。
弾力性の原則
工場や倉庫は、生産量や機械、取扱い製品の変化に対応できる「柔軟性」を持つ必要があります。製品が変わる度に大幅なレイアウト変更を行う工場は、そこにかかる人件費を考えるだけでも「無駄が多い」と考えて良いでしょう。
弾力性の原則に従い、工場は製品ラインや市場ニーズの変動に迅速に適応できる能力を求められます。例えば、製品需要が急増した際には、既存の生産ラインを変更したり、新しいラインを設けたりすることが重要です。
弾力性を持った工場では、設備やレイアウトのフレキシブルな設計が求められます。これにより、異なる製品の生産に対する適応力が向上し、必要に応じて機械を再配置することで効率的な生産が実現します。また、IoT技術を用いたスマートファクトリーの導入は、リアルタイムのデータ収集と分析により、需要に応じた生産調整を可能にします。
さらに、弾力性強化には従業員の多様な役割の理解が不可欠です。作業者が複数の工程を習得するためのトレーニングプログラムが、変化時に迅速に適応する体制を構築します。また、サプライチェーンの柔軟性も重要で、複数の供給源を確保することで材料供給のリスクを軽減し、生産計画を安定させることが求められます。
このように、弾力性の原則の理解と実行は、持続可能な成長と競争力の維持に不可欠です。この原則を基に柔軟な対応を行うことで、工場は変化に強くなり、新しいビジネスチャンスをつかむ力を高めることができます。市場の動向や技術革新に敏感であることも、弾力的な工場には欠かせない要素と言えるでしょう。
工場レイアウト改善の具体的な手順
工場のレイアウト改善を実施する際、具体的な手順に沿って進めることが重要です。
1.スペースの現状調査
スペースの現状調査は工場レイアウト改善の第一歩です。まずは、工場内の各エリアを詳細に視察し、デッドスペースや使用されていない棚や設備を特定します。これにより、スペースの無駄を明らかにし、具体的な改善の方向性が浮かび上がります。加えて、作業フローや動線の検証も欠かせません。作業者が移動する際の無駄を排除するために、ユーザーの視点から物の流れや使いやすさを考えることが大切です。データを収集し分析することで、より客観的な改善策が見つかります。現状を把握した上で改善を図ることで、作業効率が向上し、結果的に生産性の大幅な向上が期待できるでしょう。
2.物の流れに基づく動線の見直し
物の流れに基づく動線の見直しは、工場の生産性を向上させるために不可欠な要素です。まず、作業工程を視覚化し、各ステーション間の移動パターンを分析することから始めましょう。無駄な動きを排除し、作業者が効率的に必要な道具や材料にアクセスできる環境を整備することが目標です。このプロセスには、使用頻度の高い設備や資材を作業台の近くに配置することが含まれます。また、動線の改善にあたっては、安全性も考慮する必要があります。狭い通路や交差する動線は事故のリスクを高めるため、可能な限りクリアな通行を確保することが求められます。こうした取り組みを実施することで、作業の効率を大幅に向上させることができ、最終的には生産目標の達成に寄与します。
P-Q分析による物量の把握
P-Q分析は、製品の需要と供給を把握し、工場の生産計画を最適化するための強力な手法です。この分析によって、各製品の販売量(P)と生産量(Q)を比較し、実際の生産に必要な物量を明確にすることが可能になります。
このアプローチを取ることで、特に季節的な需要の変化や市場のトレンドを反映させた生産計画の立案が実現します。過剰在庫や不足のリスクを大幅に軽減し、資源の無駄を防ぐことに繋がります。
結果として、生産効率の向上やコスト削減が期待できるため、P-Q分析は生産管理において欠かせない要素となります。正確なデータ分析が、精緻な生産計画を支え、工場運営の安定性を高めるのです。
3.機械設備配置の設計検討
設備配置の設計検討は、工場の生産効率を最大限に引き出すための重要な要素です。最適な配置を実現するには、まず各工程や作業の流れを詳細に分析することが必要です。特に、動線を重視することで、作業者が無駄なく移動できる環境を整えることが可能となります。
例えば、材料の供給エリアから使用箇所までの距離を短縮し、工具や部品が必要な場所にすぐアクセスできるように配置することが挙げられます。また、それぞれの設備や作業台のレイアウトを見直すことで、作業者の負担を軽減し、習熟度を高める効果も期待できます。
さらに、柔軟な対応力を持つ配置設計も重要です。市場や製品の変化に直面した際には、迅速にラインを変更できるための構造を維持することで、工場全体の競争力を高めることができます。したがって、工場の目的や生産条件に応じた設備配置を検討することが、効率的な工場運営の鍵となります。
4.レイアウト案の検証と選定
レイアウト案の検証と選定は、工場運営において生産性向上に直結する重要なステップです。まず初めに、提案されたレイアウト図や図面を作成、実際の環境でシミュレーションし、動線の流れや作業員の動きがスムーズかどうかを確認します。このプロセスでは、関係者からのフィードバックを得ることが重要です。また、異なるレイアウト案を比較し、各案のメリット・デメリットを明確にすることで、最も効果的な配置を特定することが可能です。ツールを使ってレイアウト案を作成して比較・検証する際は、エクセル・3DCADや専用ソフトを用いてシミュレーションを行うことも効果的です。
さらに、コストや導入後のメンテナンスの観点も考慮して選定を行う必要があります。ここで信頼できるデータを基にした定量的な分析が効果を発揮します。実際の生産効率や時間の短縮、作業ミスの削減など、具体的な数値を持つことで、関係者を説得しやすくなります。確実な検証を経た上で最適なレイアウトを選ぶことが、工場全体の運営効率に大きく貢献します。
5.レイアウト変更後の状態確認と調整作業
改善後の状態確認と調整作業は、レイアウト変更の効果を最大化するために不可欠なステップです。まず、変更したレイアウトが実際の作業環境に適合しているかを観察し、作業者からフィードバックを受けることが重要です。これにより、潜在的な問題や改善点を早期に発見できます。
次に、業務フローや動線が円滑に機能するかテストし、必要に応じて微調整を行います。例えば、物品の保管場所が不便であれば、アクセスを改善するための再配置を検討します。また、作業者の負担を軽減するための設備の位置調整も効果的です。定期的なチェックを行い、進捗を記録することで、レイアウトの改善が持続可能なものになります。これらの取り組みを通じて、工場全体の生産性向上が期待されるでしょう。
6.レイアウトの定着化のための取り組み
レイアウトの定着化を図るためには、継続的な教育とモニタリングが不可欠です。新しいレイアウトがスムーズに運用されるためには、作業者への周知活動や定期的なトレーニングを実施することが重要です。具体的には、改善点や注意事項を明確にしたマニュアルを作成し、作業者全員がアクセスできる場所に掲示することが効果的です。
また、現場のフィードバックを大切にし、定期的に状況をレビューすると良いでしょう。作業者の意見を反映させることで、レイアウトが実際の運用に適しているかを確認し、必要があれば柔軟に調整します。さらに、KPI(重要業績評価指標)を設定し、目標達成度を測定することで、意識を高めると同時に改善のモチベーションを維持できます。このような取り組みの積み重ねが、しっかりとした定着化を促進し、工場全体の生産性向上に繋がるのです。
工場レイアウトの種類
工場のレイアウトには主にジョブショップ型、ライン型、セル型、据え置き型の4つのタイプが存在します。 それぞれのレイアウトは、特定の生産ニーズや製品の種類に応じて適切に選ぶことが重要です。 それぞれのレイアウトには特徴があり、工場の目的や生産形態に応じた選び方が求められます。これを適切に選定することで、生産性や効率性の向上につながります。
ジョブショップ型(機能別)のレイアウト
ジョブショップ型(機能別)のレイアウトは、多品種少量生産に特化した効率的な生産方式です。この形式では、同じ機能を持つ機械や設備がまとめられ、異なる製品が専門のエリアで加工されます。ここでは、顧客の要求に応じたフレキシブルな対応が可能となるため、特注品やさまざまな注文内容に迅速に対応できます。
適切に設計されたジョブショップ型では、工程間の流れを最適化することで、作業者の移動回数を削減し、無駄な時間を排除する仕組みが重要です。また、各作業ステーションの近くに必要な工具や材料を配置することで、作業効率を高め、災害のリスクを軽減することが可能です。こうした工夫により、全体の生産性が向上し、結果的にはコスト削減にも繋がります。つまり、ジョブショップ型のレイアウトは、変化に対応しやすく、柔軟な生産環境を提供するための重要な要素なのです。
ライン型(製品別)のレイアウト
ライン型(製品別)のレイアウトは、大量生産を行う工場にとって最適な選択肢です。この形式の最大の特長は、作業が順序立てて配置されているため、効率的な生産プロセスを実現する点にあります。各工程が明確に設定されているため、作業者は特定の手順に従い、スムーズに作業を進めることが可能です。
このレイアウトは、特に同一製品の大量生産時にコスト削減や生産速度の向上をもたらします。自動車や加工食品など頻繁な生産工程の変更が少ない環境であれば、安定した品質を維持しやすいのも魅力的です。ただし、ラインの柔軟性が欠けるため、製品変更に対する慎重な計画と準備が不可欠です。全体の効率を最大化するために、ライン型レイアウトの導入は重要な戦略となります。
セル型(グループ別)のレイアウト
セル型(グループ別)のレイアウトは、効率的な生産活動を促進するための効果的な手法です。このレイアウトでは、関連する作業や工程を一つのセルにまとめ、作業者が互いに協力しながら作業を進めることができます。特に、多様な製品を少量生産する際に、その効果が発揮されます。
この形態のメリットは、作業の流れをスムーズにし、製品の製造時間を短縮する点です。また、作業者同士が近くにいるため、迅速な情報交換や問題解決が可能となります。これにより、チームワークを強化し、作業の精度向上にも寄与します。
さらに、工程変更が容易なため、市場のニーズや顧客の要望に迅速に対応することが可能です。設備の配置を工夫し、高度な柔軟性を持たせることで、変化の激しい環境においても安定した生産が実現できます。セル型のレイアウトは、現代の製造業において不可欠な選択肢として、多くの工場で活用されています。
据え置き型(固定式)のレイアウト
据え置き型(固定式)のレイアウトは、特に大型設備や重機の製造において効果的です。この形式では、設備が固定され、作業者や材料がそれに応じて動くため、大規模プロジェクトに適しています。固定式の特性により、作業者は特定の位置で専門性を発揮しやすく、効率的に作業を進めることが可能です。また、作業の流れが明確になり、各工程での役割がはっきりしているため、コミュニケーションの質も向上します。
据え置き型のレイアウトでは、出入り口や通路の配置に特に配慮が必要です。大型機械や重い部品の移動が頻繁に発生するため、安全管理を徹底するとともに、作業環境を整備することが必須です。このように、固定式レイアウトは生産性向上につながる可能性が高いですが、慎重な計画と実行が求められます。
最適な工場レイアウトを選ぶ際のポイント
前項にて様々な工場レイアウトの例をご紹介しました。 数あるレイアウトバリエーションから自社に最適なレイアウトを選ぶための考え方・工場レイアウトを最適化する際に留意すべきポイントを4つに絞ってご紹介していきます。
生産性向上に繋がる要素の確認
生産性向上に繋がる要素の確認は、工場運営において極めて重要です。まず、作業プロセス分析を通じて、ボトルネックを特定することが求められます。これにより、時間や資源のロスを最小化し、効率的な生産ラインを構築できるようになります。
次に、作業環境の快適さも要素の一つです。作業者が集中できる環境を整えることで、ミスを減少させ、作業効率を向上させることが可能です。さらに、従業員の意見を取り入れることで、現場での改善点を見出しやすくなります。
動線を短縮し、設備配置を見直すことで、物の流れをスムーズにし、作業時間の短縮が実現します。 これらの要素を一つ一つ丁寧に確認し、改善策を計画することが生産性向上に繋がります。
作業効率と動線の連携を重視する
工場の作業効率を最大化するためには、動線の設計が不可欠です。作業者が必要な道具や材料に迅速にアクセスできるよう、動線を意識したレイアウトが求められます。特に、頻繁に使用する設備や作業ポイントを近接させることで、移動距離を最小限に抑えることが可能にします。これにより、作業時間の短縮が実現し、生産性向上に寄与します。
混雑した通路や重複した動線は、事故や作業ミスを引き起こすリスクを増大させるため、シンプルで明確な動線設計が求められます。作業工程を可視化し、理想的な流れをもとにレイアウトを見直すことが効果的です。
保存場所の計画的配置
効率的な工場運営を実現するためには、保存場所の計画的な配置が不可欠です。適切に配置された保存場所は、作業者が必要な物品を迅速に取り出せることを保証し、作業の遅延を防ぎます。これにより、製品の移動や作業フローがスムーズに進むため、全体の生産性が向上します。
また、使用頻度に基づいて保存場所を分類することで、最も必要とされる資材や部品をアクセスしやすい場所に配置するのが理想的です。高頻度で使用されるアイテムは作業ライン近くに、逆に低頻度のものは倉庫の奥に位置させることが有効です。さらに、保存場所を整然と管理し、バーコードやラベルを使用して在庫を簡単に確認できるシステムを導入することで、時間の節約やミスの削減につながります。
エリア分けによる運用効率化
エリア分けは、工場の運用効率を高めるために極めて重要な手法です。各作業エリアを明確に定義することで、作業者が必要な資材や設備に迅速にアクセスできる環境が整います。これにより、無駄な移動が減り、作業のスピードが向上します。衛生管理が必要な食品工場などではトイレの位置なども検討しましょう。
また、エリア分けは部門間の連携を強化する効果も持っています。関連する作業や部署を近接させ、事務所の配置についても検討することで、情報共有やコミュニケーションが円滑になります。特に、迅速な意思決定が求められる環境において、こうした連携の強化は競争力の向上に直結します。
工場の効率的運用に向けたレイアウト改善のまとめ
工場の効率的運用には、レイアウト改善が欠かせません。適切なレイアウトは、生産性や作業効率の向上に大きく寄与します。まず、現状の動線や作業工程を見直し、無駄な動きを排除することが重要です。作業者が簡単に必要な物品にアクセスでき、また設備への移動もスムーズに行えるような配置を考える必要があります。
次に、エリアの適切な分け方も重要な要素です。関連する業務や作業が隣接していると、部門間のコミュニケーションが円滑になります。これにより、情報の流れがスムーズになり、業務の効率が向上します。また、安全対策を考慮したレイアウトも不可欠です。作業者が安心して働ける環境を整えることで、事故やトラブルのリスクを軽減できます。
さらに、レイアウトの改善を実施した後は、その効果を継続的にモニタリングすることが求められます。改善点を定期的に見直し、フィードバックを受けて適宜修正することで、持続的な効果を得ることができます。これにより、工場運営の効率化が図られ、企業全体の生産性向上に繋がります。
総括すると、工場のレイアウト改善は多くの要素を考慮しつつ、効果的に行う必要があります。これによって、作業環境の向上や利益の最大化が実現できるでしょう。各ポイントに注力し、継続的な改善に努めることが、効果的な工場運営への鍵となります。
工場・倉庫の暑さ対策に『クールサーム®』
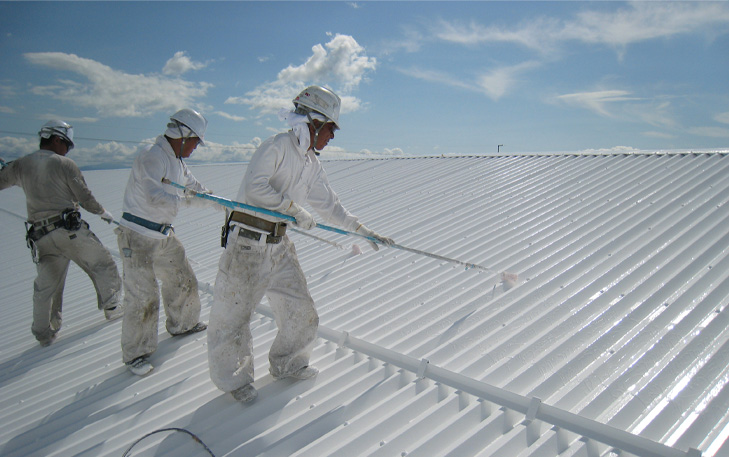
屋根に塗るだけで空調代を削減!※1
可視光線、近赤外線のほとんどを反射し、また一部吸収した太陽エネルギーを遠赤外線として放散、さらに遮断層を作り熱伝導を防ぐ、といった特性を持つNASAが開発した特殊なセラミックで屋根や壁面を塗装。劣化の原因となる紫外線もカットして、断熱効果は長期間(10年以上※2)持続可能。コスパの高い断熱素材です。
※1 理想科学工業㈱霞ヶ浦工場の実例を元に、イメージ表示し得られたデータを元に室内空間の温度上昇を抑制することから、空調設備の温度を上げることで電気代等の削減が期待できます。
※2 クールサーム®の実証実験にて10年以上の耐久性を確認しています。詳しくは弊社スタッフまでお問い合わせください
SAWAMURAについて
1950年の創業以来、地域に貢献すること、お客様の事業の発展に寄与することを目標に
さまざまな建築物を竣工してきました。1998年よりシステム建築事業をスタート。
豊富な経験と実績をもとに、さまざまなご要望にお応えします。
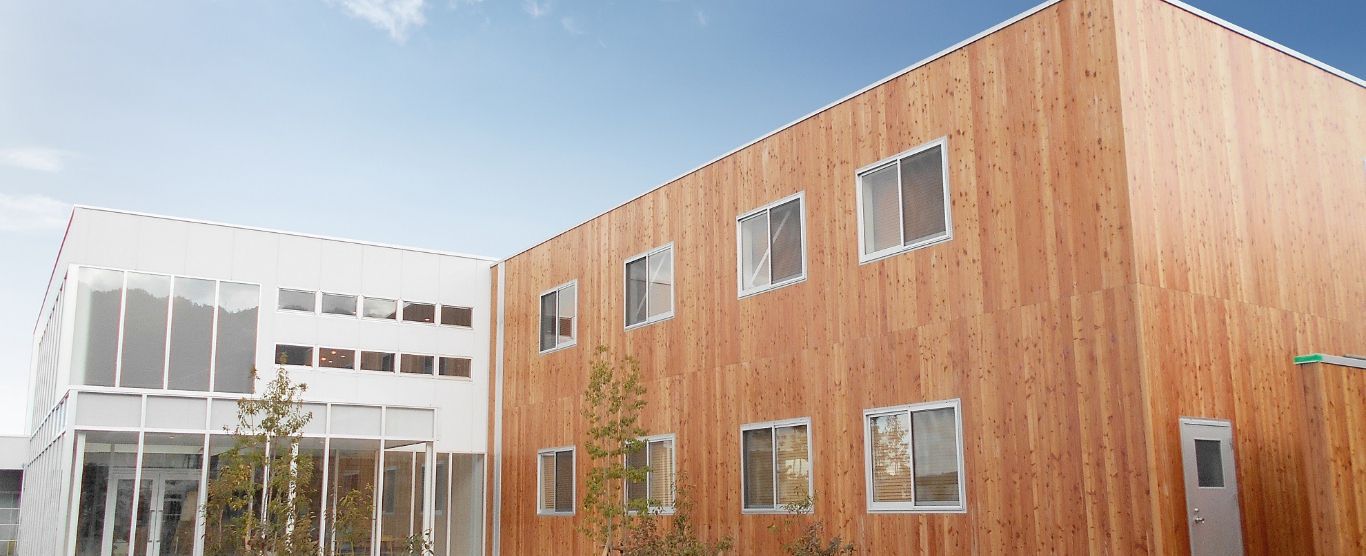
関西No.1のシステム建築実績。
積み重ねた施工実績とノウハウで、
確かな精度を保証します。
- 2020年
- 関西ブロック優秀ビルダー賞1位
- 2019年
- 関西ブロック優秀ビルダー賞3位
関西ブロック年間販売実績 第1位 5年連続受注賞
アティブビルダー銀賞受賞 - 2018年
- 関西ブロック年間販売実績 第3位 5年連続受注賞
アクティブビルダー銅賞受賞 - 2017年
- アクティブビルダー銅賞受賞
- 2016年
- アクティブビルダー銅賞受賞
- 2015年
- アクティブビルダー 銅賞受賞
- 2012年
- 連続販売年数15年達成
- 2013年
- 15年連続受注賞
- 2008年
- 10年連続受注賞 2005年 5年連続受注賞
- 2004年
- 優秀ビルディング
資格所有者
-
一級建築士 13人
二級建築士 41人
一級建築施工管理技士 29人
一級土木施工管理技士 10人 -
宅地建物取引士 19人
設備設計一級建築士 1人
土地家屋調査士 1人
一級建設業経理士 2人
中小企業診断士 1人
会社概要
社名 | 株式会社澤村 |
---|---|
本社 | 〒520-1121 滋賀県高島市勝野1108番地3 TEL. 0740-36-0130(代) FAX. 0740-36-1661 |
大津オフィス | 〒520-0242 滋賀県大津市本堅田三丁目33-16 エルミナ リアン 2F TEL. 077-572-3879 FAX. 077-573-8384 |
敦賀オフィス | 〒914-0811 福井県敦賀市中央町一丁目8-10 TEL. 0770-22-6005 FAX. 0770-47-6405 |
資材センター | 滋賀県高島市勝野873-1 |
創業 | 昭和25年12月6日 |
資本金 | 50,000,000円(グループ全体) |
従業員数 | 182名(グループ全体)※2024年10月1日現在 |
売上高 | 63億円(グループ全体)※2024年9月実績 |
営業種目 | 建築一式、土木一式、大工工事、水道施設工事、とび・土工工事、造園工事、左官工事、石工事、屋根工事、タイル・れんが・ブロック工事、鋼構造物工事、鉄筋工事、舗装工事、板金工事、ガラス工事、塗装工事、防水工事、内装仕上工事、熱絶縁工事、建具工事、宅地建物取引業、建築・土木設計、土地活用 |
許可・登録 | 〈建設業許可〉 滋賀県知事許可(特・般-3) 第80123号 〈一級建築士事務所〉 滋賀県知事登録(カ) 第126号 〈宅地建物取引業者〉 滋賀県知事登録(12) 第1267号 |
取引銀行 | 滋賀銀行 高島支店 関西みらい銀行 安曇川支店 滋賀県信用組合 安曇川支店 |
関連会社 | 株式会社トータル・オーガニック・プランニング 沢村ホーム株式会社 |
工場・倉庫建築について
どうぞ、お気軽にお問い合わせください。
- これから計画を始める方
- おおよその予算やスケジュールが知りたい方
- 敷地調査や提案を希望される方